WILLKOMMEN
Einst stand der Name INTERCEPT Technology™ ausschließlich für eine, auf Kupfer basierende, Korrosionsschutzmethode, die völlig auf sekundäre Schutzmittel wie Öle, Wachse oder Papiere verzichtet und in einer Vielzahl von Industrien angewendet wird.
Mittlerweile sind wir weit mehr als das: INTERCEPT™ hat sich weiterentwickelt und ist zu einem weltweit vernetzten Unternehmen gewachsen. Unser Fokus liegt heute auf smarten Gesamtverpackungskonzepten sowie hochmodernen, technischen Lösungen, die zur Verschlankung globaler Lieferprozesse beitragen. Wir analysieren jeden einzelnen Schritt entlang der Supply Chain, identifizieren Kostentreiber während des Liefer- und Lagerungsprozesses und implementieren ausgefeilte Verbesserungslösungen.
Vereinfachte Prozesse – Bessere Lösungen – Zuverlässiger Schutz – das ist INTERCEPT!
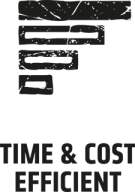
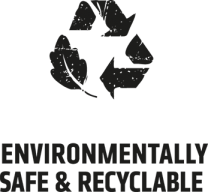
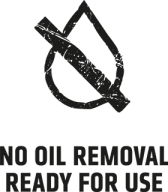
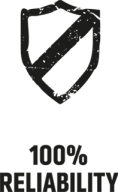